Extreme Energy Surety – Resilience in Demanding Environments
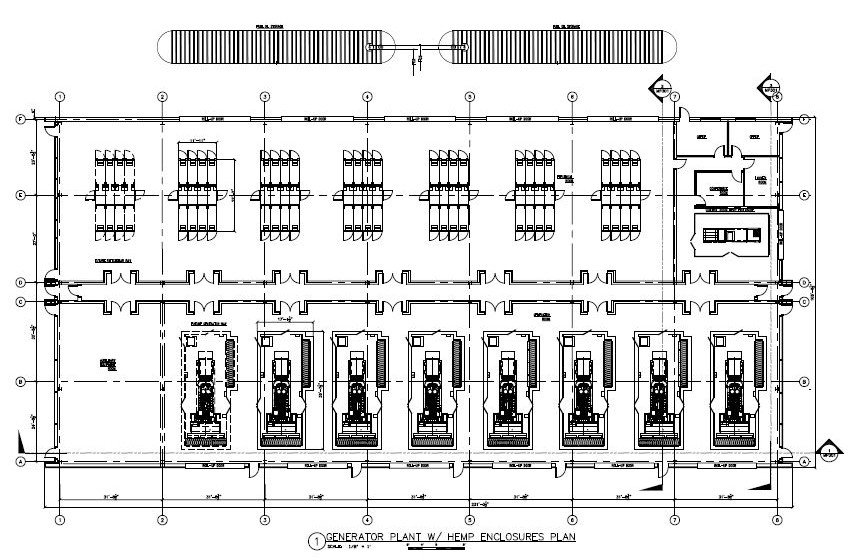
Power Generation Plant (PGP) General Arrangement
Regardless of geography, energy resiliency is always impacted by weather. Weather extremes in all locations lead to challenges and problems in generation, transmission, and local distribution.
Providing energy surety and resiliency in one of the planet’s harshest environment required a differentiated and unconventional approach in determining fuel types, sourcing equipment, developing construction strategies, and establishing long-term operation and maintenance plans.
Extreme operating conditions require that the entire development-design-build-operate continuum be integrated with early-stage design and development decisions and be “back-fed” with subject matter expertise that addresses later-stage issues such as long-term maintenance and operation.
This holistic approach to early development activities ensures that critical resiliency issues and challenges related to the future stages of the project are addressed early-on where maximum ability to affect change occurs.
This differentiated design and development approach led to a design basis for this extreme energy surety plant that consisted of a state-of-the-art power conditioning and standby microgrid facility situated within a 20,000 square foot building with adjacent electrical interconnect building and support areas.
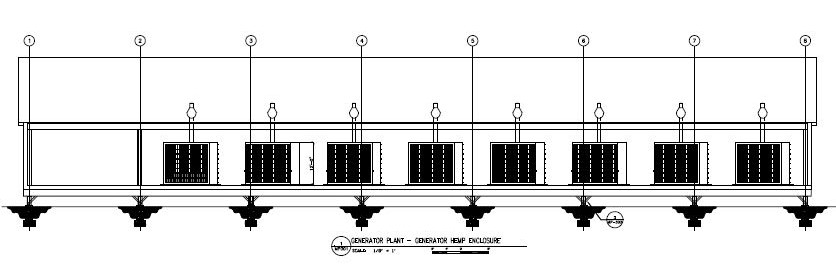
PGP Truck Bays for Modular Generators
The plant’s design consisted of an arrangement of six 2 MW standby diesel generators mechanically coupled to rotary UPS (flywheels) providing both continuous conditioning of normal utility power and the ability to seamlessly transfer to standby generation during fault conditions or when operationally mandated.
A primary design criteria for all the proposed prime mover generation equipment and gear was to have high immunity to leading power factors.
In extreme weather environments, construction windows are short and uncertain, so in order to accommodate fast-track construction schedules, modular fabrication approaches are used that comply with various DoD Unified Facility Criteria (UFC). Specifically, UFC 3-130-04-compliant (Foundations for Structures: Arctic and Subarctic Construction) foundations that would incorporate a pier-supported system were included in the design. All footings and piers required for future build-out would be installed during the first phase of construction, allow for building completion during non-summer months.
Proposed Project Features
- Multi-Unit / Multi-Source
- 99.999% Guaranteed Availability
- Black Start & Long-Term Island Capability
- Microgrid Power Quality within ITIC
- Prefabricated Skids
- Multiple Redundant Systems (N+2)
- Modular HEMP Enclosures
- Off-Site Fabrication & Testing
- Modular & Duplicative
- Arctic Construction Standards (UFC 3-130-04)
Stringent Requirements Demand Exacting Design Criteria
Fort Greely’s climate is classified as subarctic, but it is characterized by a wide range of temperatures with very cold winters and short warm summers. Winter lasts from mid-October until mid-to-late April. The nearest population center is Fairbanks, which is commonly known as America’s coldest city. Average winter low temperatures range from −15 to −25 degrees F, but extremes can range from −60 to −75 degrees F in the winter, with temperatures approaching 90 degrees F in the summer.
These widely varying temperature extremes drive design criteria and construction limitations that are highly unique requiring innovative solutions. Properly implementing a design solution to handle these extremes without disrupting mission operations require extensive measurement of baseline conditions to acquire sufficient empirical data to analyze and perform simulations prior to establishing a basis of design.
Pre-Fabricated Modular Approach Streamlines Schedules and Lowers Costs
The economics of implementing extreme energy surety projects in demanding conditions with short construction windows and sensitive environments creates intense cost pressures from any number of uncertainties related to project development, delivery, and on-going operation. Common to many of these risks is the uncertainty of onsite labor efficiencies related to weather, site access, and the availability of qualified personnel. These uncertainties can extend over the lifetime of the project, creating initial construction cost pressures that escalate post-commercial operation costs during the performance period.
Standardized modular designs address many of these extreme environment issues and mitigate risk involved with construction and long-term operation of system assets. Using modular approaches in extreme environments reduces design, schedule, and cost uncertainties, and as a result, improves project economics and viability. Standardized designs also reduce front-end engineering efforts, lower engineering cost, expedite development cycles, and allow for faster construction kickoffs. And modular energy plant designs reduce on-site disruption while improving quality control by increasing the proportion of fabrication work performed in a controlled shop environment versus in the extreme weather-impacted field.
Pre-Engineered / Pre-Assembled / Pre-Tested
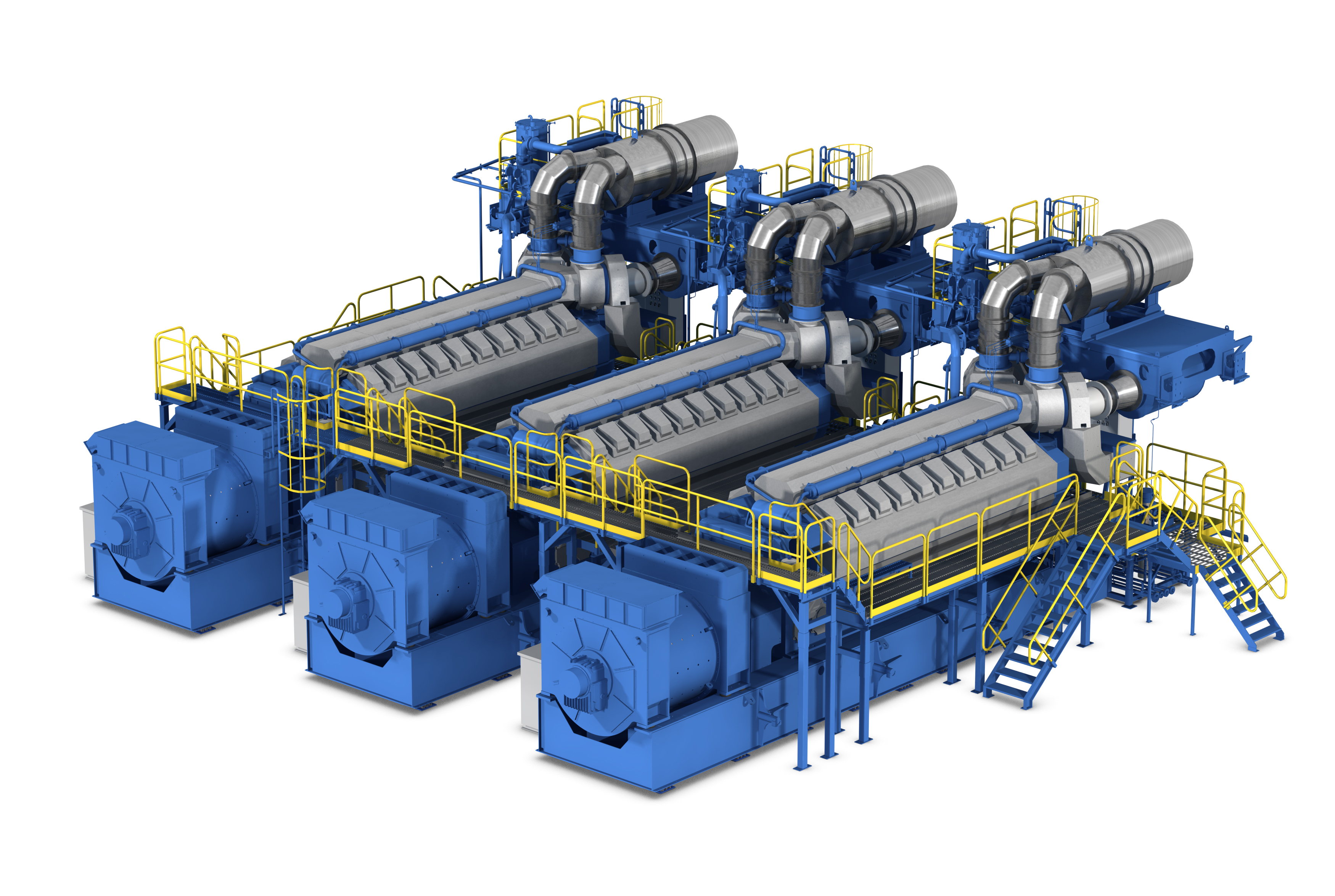
- Reduced Engineering Cost – Pre-engineered designs create engineering and fabrication efficiencies and allows for closer estimate of fabrication cost.
- Increased Fabrication Efficiencies – Field component of project cost is reduced due to the replacement of field labor tasks in shop environment which are done more efficiently with personnel who are well trained and have constructed similar modules previously (no learning curve).
- Reduced Field Labor Costs and Skill-Set Uncertainties – Field labor skill requirement is reduced due to scope complication reduction. Lower specialty contracting requirement results in lower labor costs in the field.
Reduced Contingencies – Well defined project scope and pre-engineered scope reduces the opportunity for scope creep and the associated cost creep and change orders.
Reduced Phasing Costs – The modular design lends itself better to reducing and delaying capital expenditures on infrastructure for future phases